Smart Sustainable Manufacturing research group achieves results in the digitisation of the South Holland manufacturing industry
22 December 2022
Our research group has been able to apply practice-based research in different ways within SMITZH.
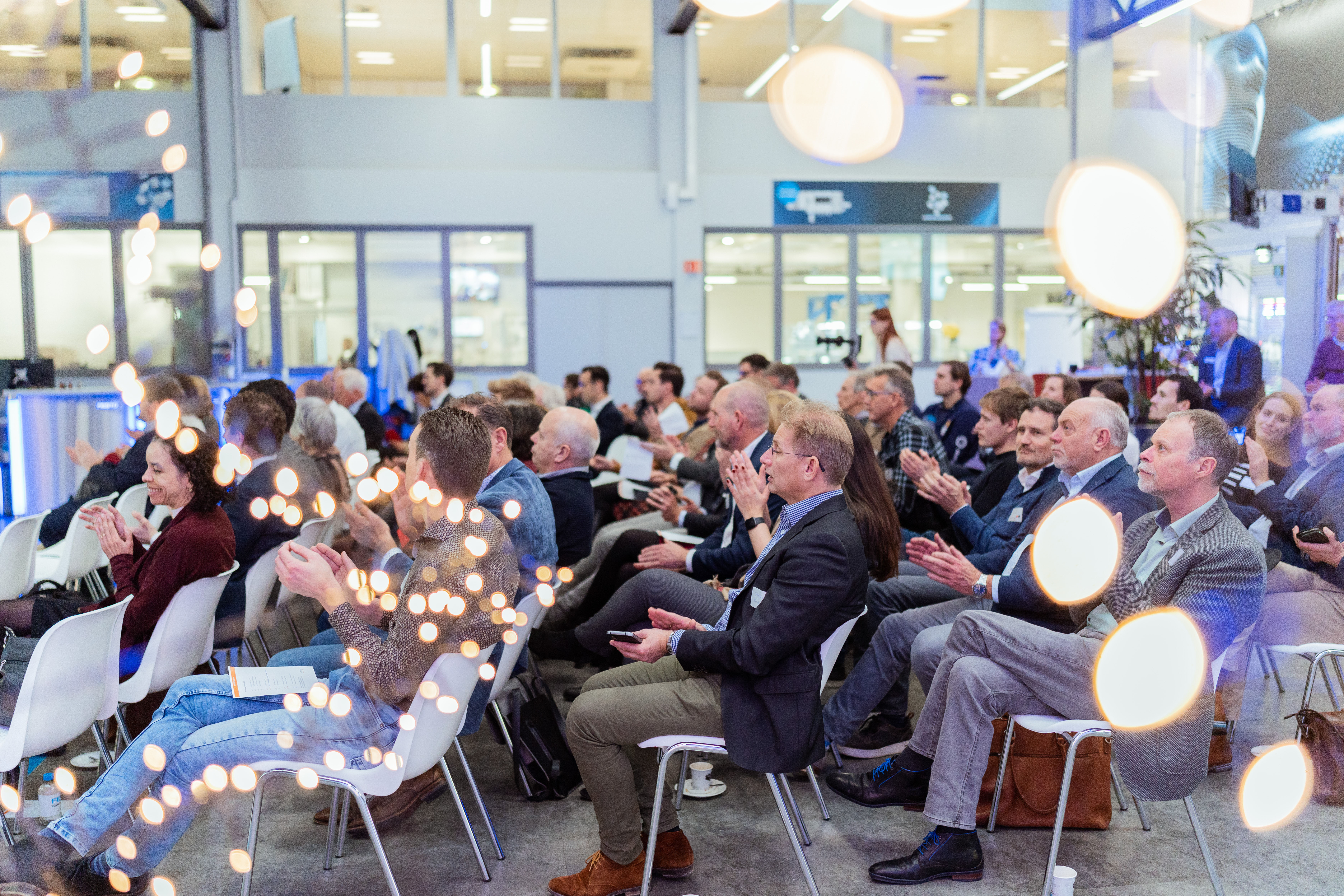
Since 2017, regional companies that wanted to produce faster, cheaper or more sustainable products could visit SMITZH (Smart Manufacturing Industrial Application Zuid-Holland), South Holland's Smart Industry Hub. The final event of this innovation programme took place on 7 December. Professor in Smart Sustainable Manufacturing, Jenny Coenen, attended the event with lecturer-researchers Edwin van Noort and Mirjam Zijderveld. They look back on their contribution in digitising the region.
Our research group has been able to apply practice-based research in different ways within SMITZH,” Jenny says. “For example, we did a digitisation scan at almost 50 companies. Rotterdam University of Applied Sciences and FME did the same, providing us with a regional picture of the state of digitalisation. That helped us to see how we could best support companies in making a digitalisation shift.
Factory-as-a-Service
“An example of such a digitisation move is Factory-as-a-Service,” Edwin explains. “By being flexible in our collaboration in smart manufacturing, we can deliver customised solutions to customers with very specific requirements. This sharing of flexible production capacity is nice, but at the same time raises many questions: how to organise it? What problems do you encounter? What are the results? We have developed some tools for this that we will publish soon.”
Circular entrepreneurship
The research group has also contributed to the theme of Smart & Circular with circular operations. “Together with TNO, we have described and compiled inspiring examples of circular manufacturing in the Circular Cases Roadmap. The roadmap contains examples that give good insight into the different forms of circularity, for example based on the R-ladder and ‘from Rethink to Recycle’. These give a look behind the scenes of other entrepreneurs,” Mirjam says.
Activating staff members
To let staff members also experience digitalisation and experiment with it, the research group developed a series of workshops on using Mixed Reality (MR). “With this technique, we can place a hologram on a (assembly) table, recognise an object and give it, for example, a different colour, or adapt instructions to the staff member’s environment or actions,” Jenny explains. “We ran a series of workshops using the Smart Kit consisting of MR and smart glasses, the so-called Hololens. This approach allowed staff members to experiment in the workplace, even out of sight of the workshop leader or colleagues. It was also useful for our research to get accessible input from the operators themselves on how they like to organise and digitise work.”
Follow-up
The fact that SMITZH has closed as an innovation programme does not mean the end of research and developments. “There will be a continuation of SMITZH in the European Digital Innovation Hubs (EDIH)”, Jenny explains. “Of course, we continue to follow this development and remain involved in SME digitisation and the Factory-as-a-Service theme through our own projects and network. This allows us to continue to contribute to the sustainability of the manufacturing industry.”
Want to know more?
Want to know more about Factory-as-a-Service, circular manufacturing or activating staff members with a Smart Kit? Please contact Jenny Coenen, [email protected] or one of the lecturer-researchers. In addition to Mirjam Zijderveld ([email protected]) and Edwin van Noort ([email protected]), Sander Limonard ([email protected]) and Pim de Jong ([email protected]) also collaborated on the abovementioned projects.